Our integrated production plant is a key performance driver for our company.
Our technical teams are experts in specialised manufacturing processes. They work with wood, metal and rope, as well as plastics and composite materials. The manufacture of raw materials involves a series of operations combining manual work and cutting-edge machinery and technology. This is all part of the play equipment manufacturing process to produce the finished parts for each of our play structures.
The combination of traditional craftsmanship with sophisticated technologies forms the backbone of our production system. It creates added value in the solutions that we develop to fulfil our clients’ quality, strength and aesthetic requirements.
The flexibility of our production line is also a plus point for the company. Our ability to adapt means that we can manufacture products with a great many variants and design unique, totally personalised structures.
Bending
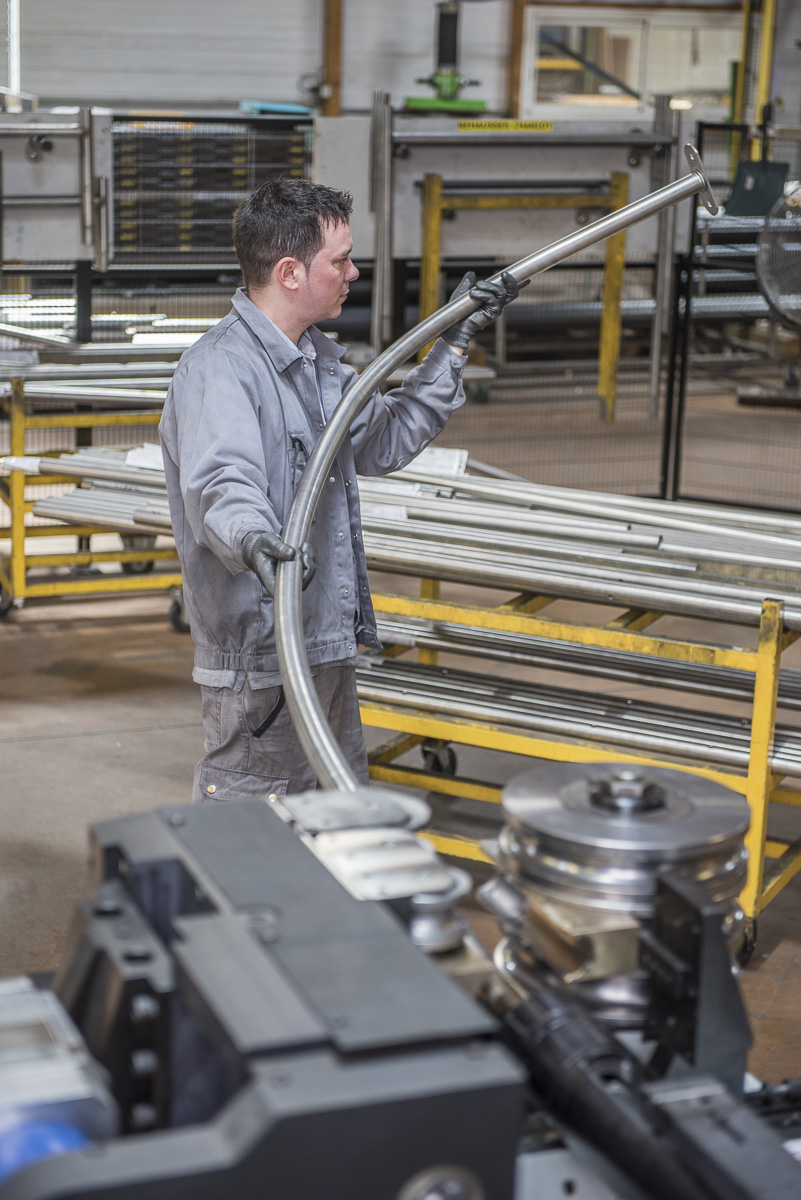
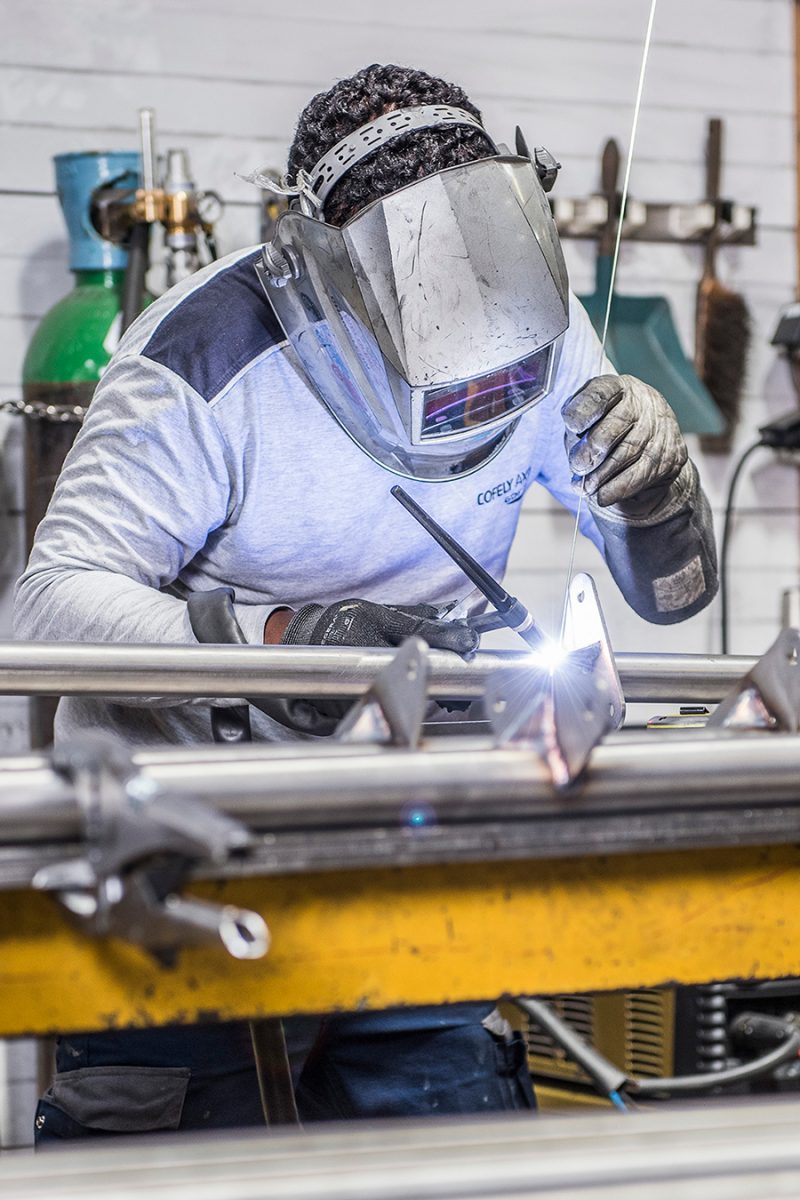
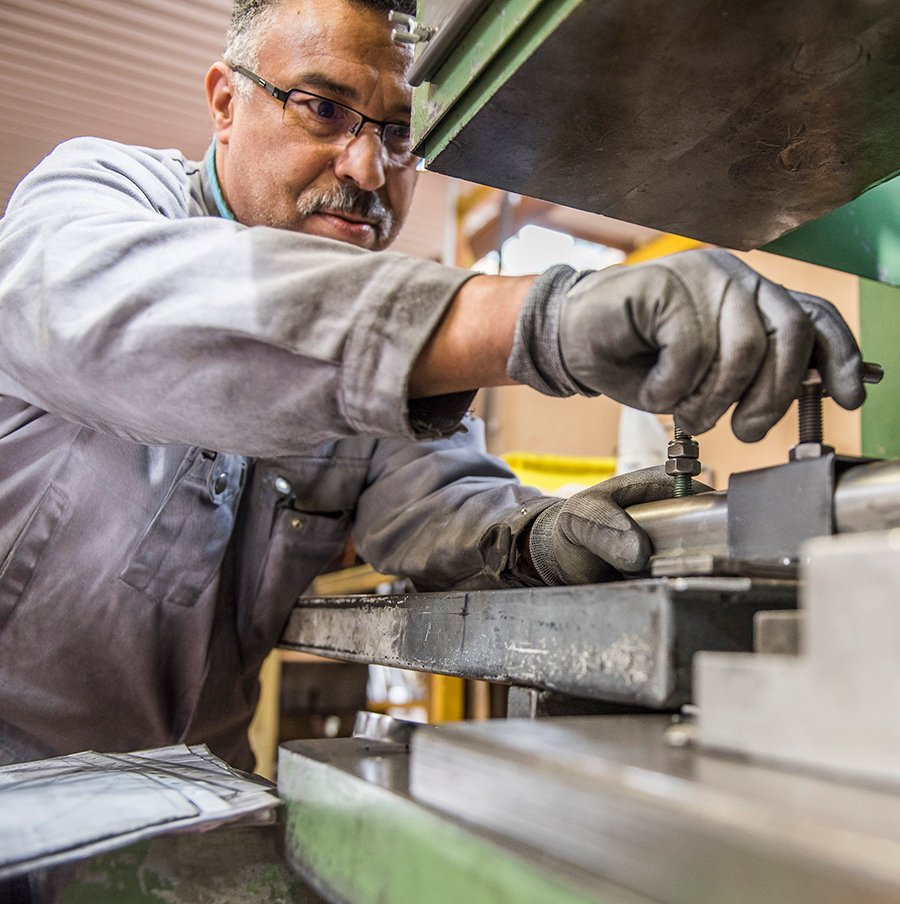
Tube bending is a skill in which our technicians are experts, working on numerically controlled bending machines. Working closely with the engineers in our design office, they shape steel to form the framework components and play elements. Numerous shapes can be produced, ranging from the simple to the complex and the inventive, but they all meet rigorous requirements in terms of combining perfect geometry with mechanical strength.
Ropes
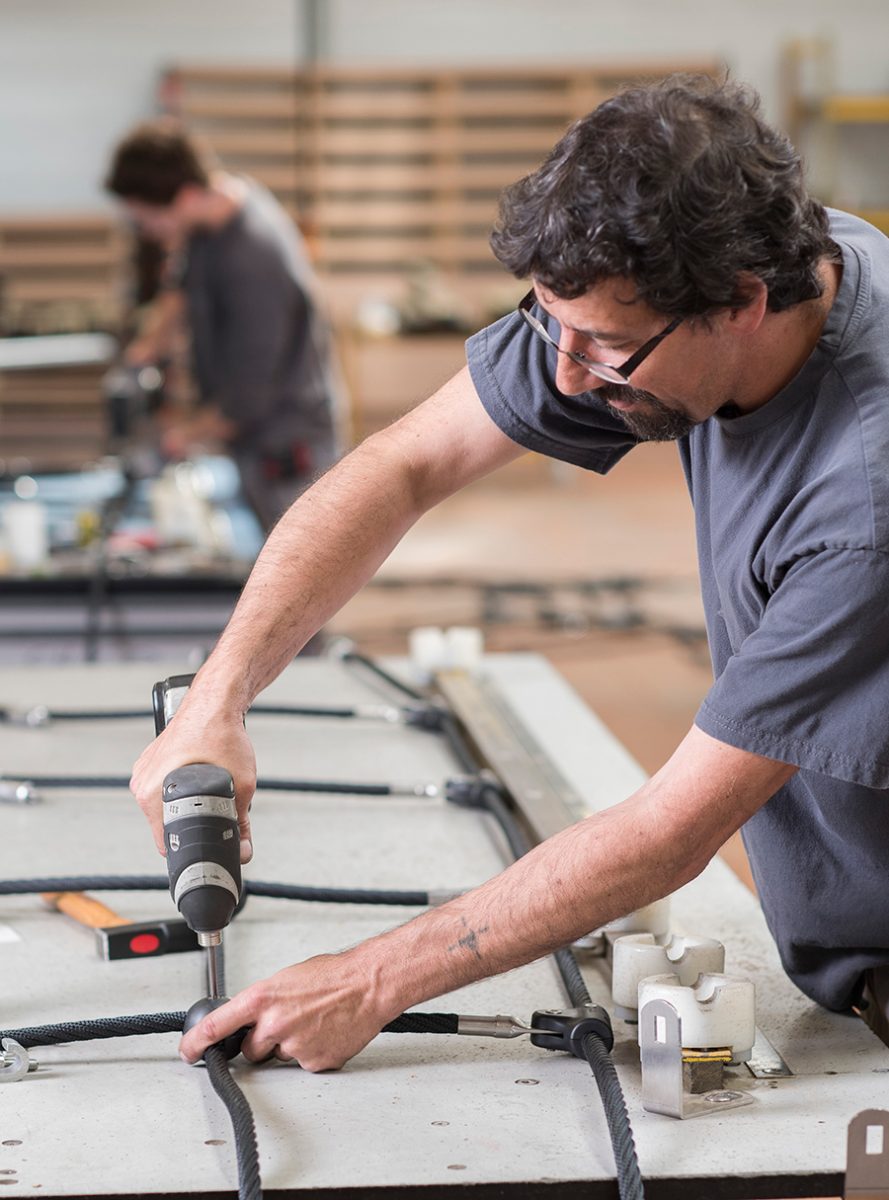
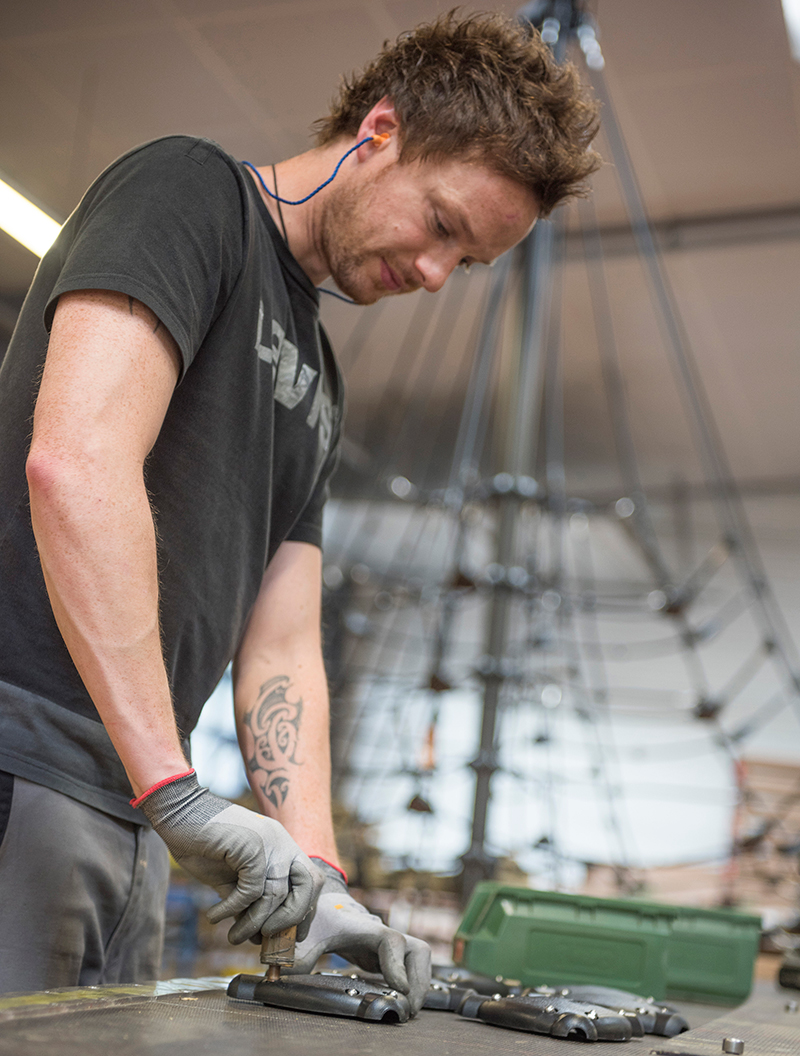
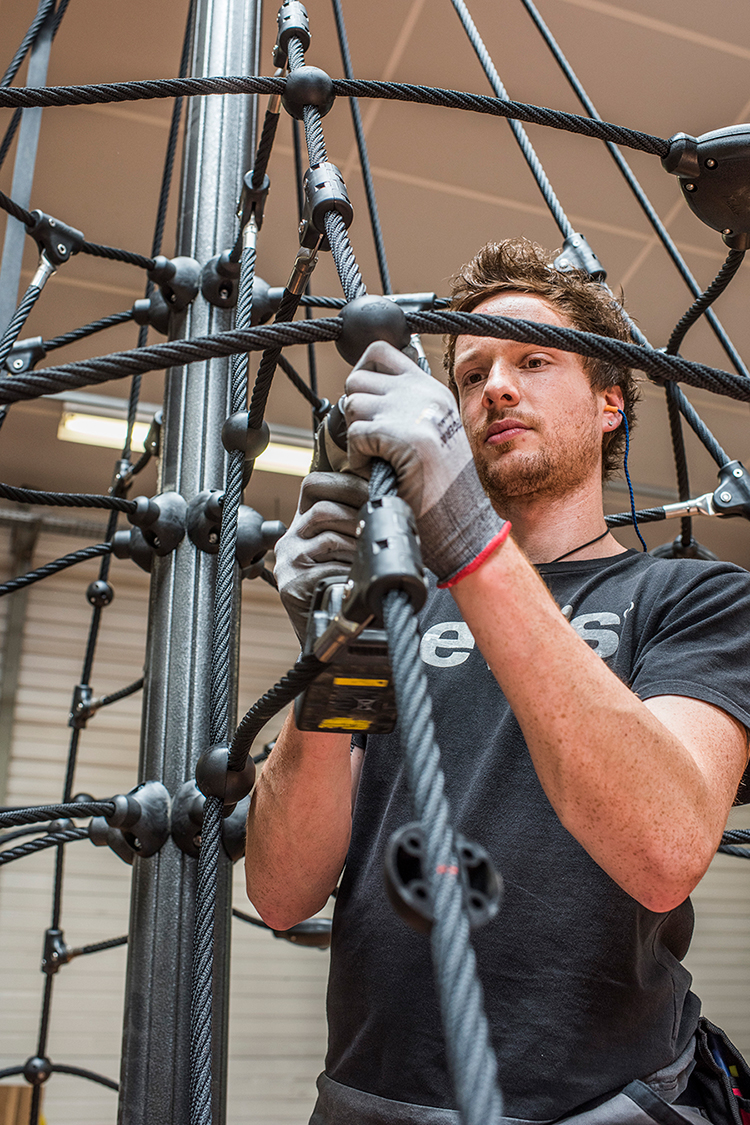
Ropework is fully integrated into our workshops.
Starting with a raw material supplied in reels, our dedicated specialist team carries out all the stages in the production process right through to the complete assembly of the element.
Using steel core ropes provides superior resistance to heavy loads and considerable flexibility in the shapes to be created. Our assembly system uses joining pieces especially developed for Proludic. Therefore we can offer a wide range of mesh types and sizes with a variety of play features.
The assembly area in our workshops is also specially adapted so that we can create large 2D and 3D projects such as our pyramid, which is over 5 meters high.
Panel cutting
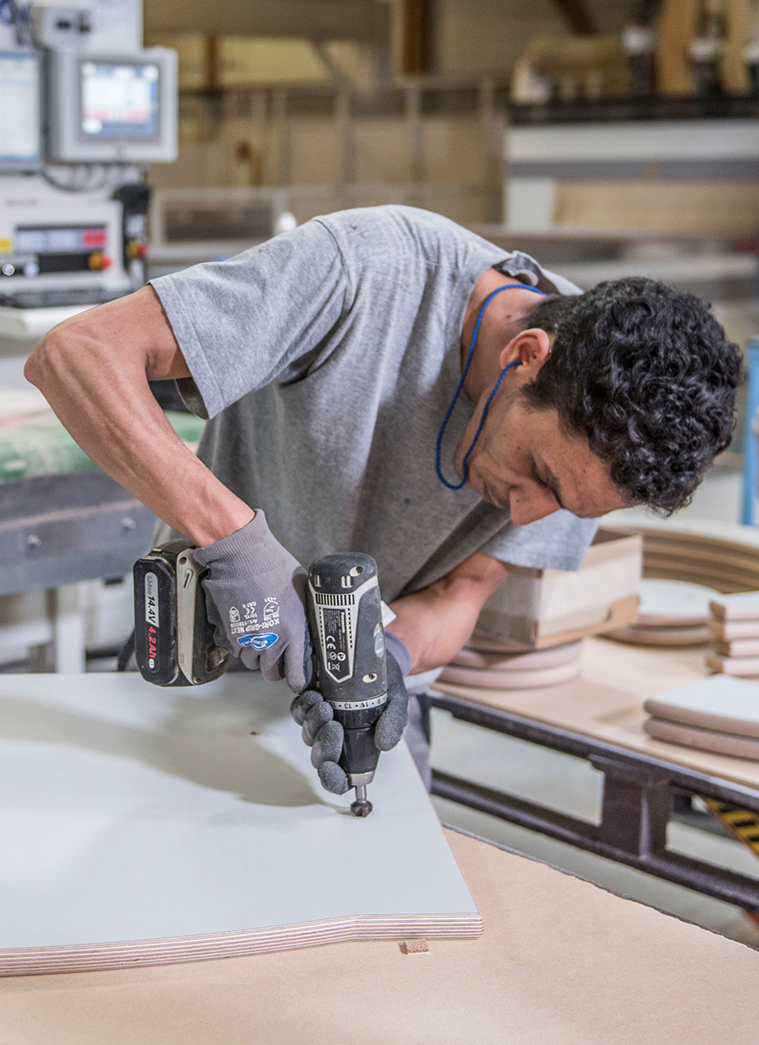
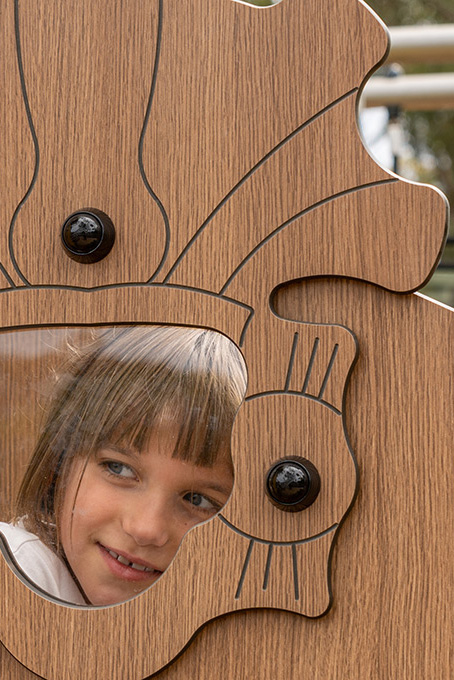
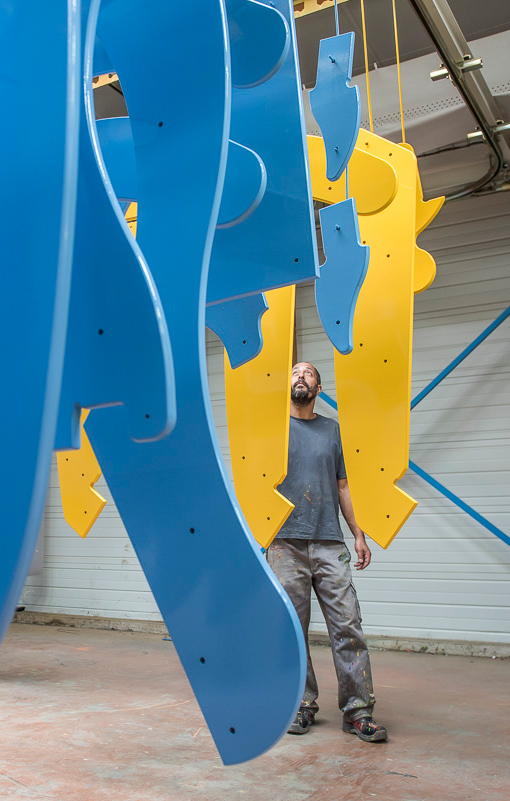
With our CNC-controlled machinery and skilled operators, we can cut panels in all 2D shapes from a wide variety of materials, including wood, compact laminate, polycarbonate and polyethylene.
This cutting expertise enables us to offer numerous ranges of play equipment with specific mechanical or physical features or looks. Additionally, we are able to meet all types of bespoke requirements.
As this activity is managed in-house, this also means that we can be quick and adaptable in our responses to clients’ requests.
Cut-out panels in some materials can also be enhanced by painting, engraving or graphic personalisation using the Grafic Games process.